
Both blades and vane’s airfoil profiles show a leading-edge, trailing edge which is a, suction side, and pressure side. This is important for optimal performance and making maximum use of the gas. The function of a vane’s airfoil (turbine or compressor) is to redirect the flow of the gas at the perfect angle to interact with the next blade. Therefore, the compressor works with a reserved principle. In the case of a compressor blade the forced rotation of the rotor (via an engine) leads to air being sucked in and compressed by the airfoils of multiple stages. In the case of a turbine blade its function is to convert the energy of the bypassing gas into a rotation of the rotor. The A irfoil is the part that interacts with the gas or steam or fluid passing by. When stabilizing and leakage are not a factor in the performance above features are not necessary. After assembly this closed ring of shrouds lowers the flow leakage of the gas or air that is bypassing the airfoil. Additionally, on the top of the shroud there can be a labyrinth design to further decrease leakage. To increase stability between the shrouds they can be connected to each other with interlocking geometrical features. The S hroud’s main purpose is to stabilize the blades/vanes via a loose connection between the neighboring shrouds. The connection of the blade/vane to the rotor/casing is usually created via a form fit or via a welded connection. By mounting the blades/vanes next to each other a big “circle” of blades/vanes is created fully and interact with the gas passing through the turbine or compressor. The shape of the root depends on the thermal and mechanical load it will need to withstand over periods of time. The design engineers must keep manufacturing costs down but at the same time enhance performance. A more complicated root design means a higher safety rating due to more “shoulders” taking the load but that will mean higher manufacturing costs because the root’s shape requires higher precision and tools and techniques in the manufacturing process. The R oot mounts the blade to the rotor or in the case of a vane it will be mounted into the casing.
While with low-pressure turbines with lower temperatures the blades tend to be exceptionally long and made from less heat resistant materials like common stainless turbine steel. But with their high mechanical loads high mass of blades at high turning speeds lead to high centrifugal forces and mechanical loads, which leads to more complex roots that is imperative for safety reasons. It also needs heat-resistant materials like nickel-based alloys. For example, with high-pressure turbines, the blades tend to be smaller, due to an environment of high heat and pressure. High, intermediate, or low-pressure applications determine the blade size and material choice. influences on the design processįirst, everything is designed to make sure that the product is in spec but manufactured in the most cost-effective way with minimal waste and maximum performance. The root, shroud and airfoil design depend on the environmental conditions the blade will need to perform in. Other factors like blade elongation (due to heat), hot temperatures, erosion, corrosion, and oxidation will determine the design too. The load that the blade would endure determines the design too. *Static loads in the form of centrifugal forces as well as torque and bending forces (in the form of air resistance) as well as dynamic loads of the moving blades. The shape of the blade is determined by the *thermal and mechanical boundary conditions which can vary a lot depending on the environment it functions and the application.
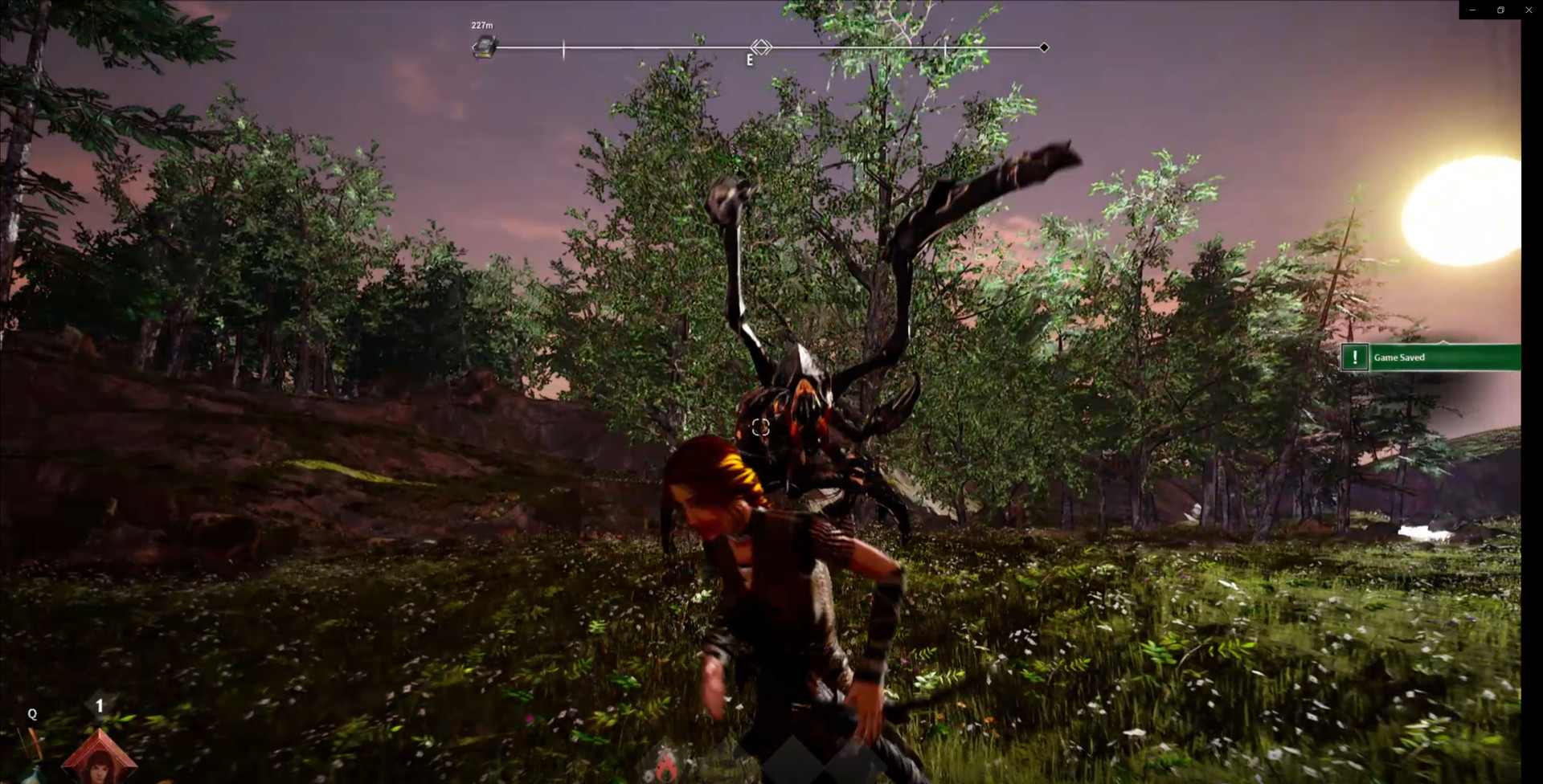
The shape and construction of the root, shroud and airfoil of the blade are determined by its application (steam turbines, gas turbines, compressor), but in essence they all function the same. This week in #allaboutblades we will look at the blade/vane that is fitted to the wheel or rotor and how it is assembled.

Previously we looked at the turbine that produces continuous power by fast-moving water, steam, gas wind, or other fluid.
